Kronalux® 2K-PU-Floor Coating 853
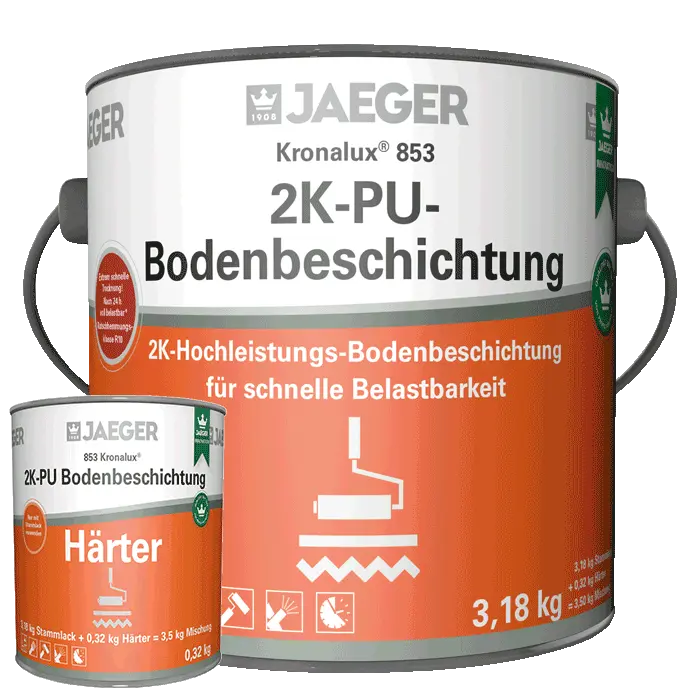
2K floor coating for industrial coatings with the highest loads
- Very good adhesion to a wide variety of substrates
- Extremely fast drying time/fully loadable after 24 h (*at 20°C/55% r.h.)
- For indoor and outdoor use
- Suitable for asphalt
- Surface is insensitive to dirt
- When loaded with forklift trucks, the dry coating does not burn
- Suitable for full-surface coatings
- Plasticiser-resistant, therefore suitable for garages
- Can harden at an object temperature of down to 5°C
- Can be tinted to RAL and NCS
Kronalux® 2K-PU-Bodenbeschichtung 853 is a high-quality two-component reactive coating for heavily used surfaces, floors and wall surfaces made of concrete, cement screed and mastic asphalt (only indoors), fibre cement and old coatings**. The surfaces can be used again immediately after a short drying time of 24 hours*. This means that floor coatings can also be applied at low temperatures! The product is largely resistant to water, petrol and diesel fuel, road salt, diluted alkalis, weak acids and common household cleaners. Kronalux® 2K-PU-Floor Coating is available in the colours pebble grey and stone grey.
At 20°C / 55% relative humidity. Check compatibility/adhesion in advance.
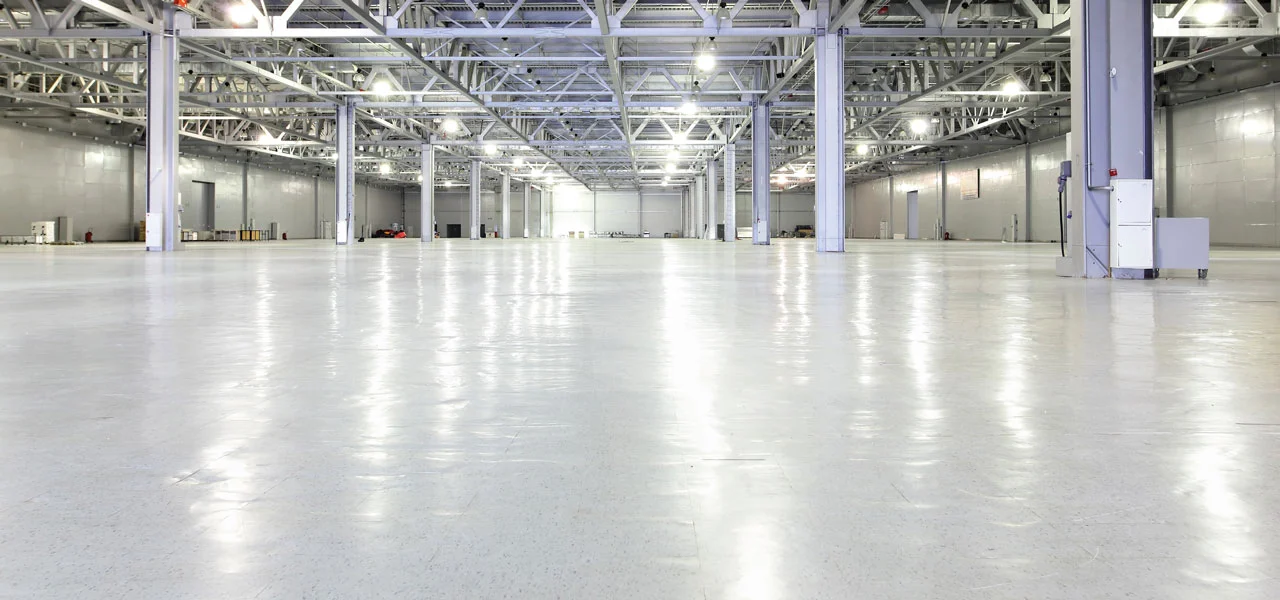
Preparation of the substrate
Coatings on concrete, screed
Mineral substrates must be well set before painting work begins; new concrete must be at least 4–6 weeks old. The substrate must be dry, clean, grease-free and load-bearing. Loose and crumbling layers must be removed. Concrete and screed must still have sufficient absorbency to ensure adhesion. Any cement paste or sinter layers on the surface must be removed by sandblasting, milling or treating with dissolved citric acid. Oily concrete surfaces that have already been used are best cleaned by brushing with Jaeger 080 Special Cleaner or alkaline cleaning agents. The surface should then be washed with plenty of water or a steam cleaner. Allow the surfaces to dry thoroughly afterwards. Adhesion is affected by moisture on the back.
Magnesite or hard concrete surfaces and non-absorbent substrates
Remove wax or care products with nitro-thinner. Sand the substrate or acidify with citric acid and then wash with water. If necessary, apply a coat of Kronalit® Epoxy-Primer 819 + 5% Katalysator 883 to achieve better adhesion.
Coatings on steel
The substrate must be dry and clean, free of rust, mill scale, grease and chemical contamination. Use Jaeger Multigrund 715 as corrosion protection.
Sand down old coatings
We recommend a preliminary test to check adhesion.
Processing conditions
During the entire processing and drying time, the material, substrate and air temperature must not fall below 5°C or exceed 30°C. The humidity should be between 30% and 75% relative humidity during the entire time.
No drying without hardener.
For safety reasons, no food may be stored in the rooms to be coated during the painting work and during the drying time.
Paint structure
1st coat: 2K PU floor coating 853 + 5-15% thinner 97.
2nd coat 2K PU floor coating 853 + 0-10% thinner 97. Apply the 2nd coat after no more than 48 hours (20°C)
Coating structure: for R12 slip resistance
1st coat: Prime the mineral substrate with special priming resin 864 according to the TM
2nd layer: scatter the damp coating with 50% drop-on material 759
3rd layer: 2K PU floor coating 853 + 5-15% thinner 97
4th layer: 2K PU floor coating 853 + 0-10% thinner 97
Application of the second coat after no more than 48 hours (20°C)
Drying (55% r.F.) | resilient |
At 5°C | approx. 6 days |
At 10°C | approx. 5 days |
At 20°C | approx. 24 hours |
At 25°C | approx. 20 hours |
At 30°C | approx. 14 hours |
All temperature information refers to the floor temperature. This can deviate significantly from the air temperature. High layer thicknesses, high humidity and stagnant air can lead to longer drying times. Do not use in living areas.
Technical data
Mixing ratio: 10 : 1 (parts by weight) with hardener 853 000H
Pot life: approx. 2 hours at 20°C (shorter pot life at higher temperatures)
Tools: Solvent-resistant roller with 6mm pile, e.g. made of polyamide.
Tool cleaning: with Jaeger Special Thinner 97.
product data
spreading rate
paint/roll | spraying |
---|---|
2,5 – 4 m²/kg |
item number/shade
item number | shade |
---|---|
853-7032 | pebble grey |
853-7030 | stone grey |
size of trading unit/box content
size of trading unit | box content |
---|---|
3,5 kg | 1 |
9 kg | 1 |